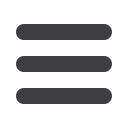
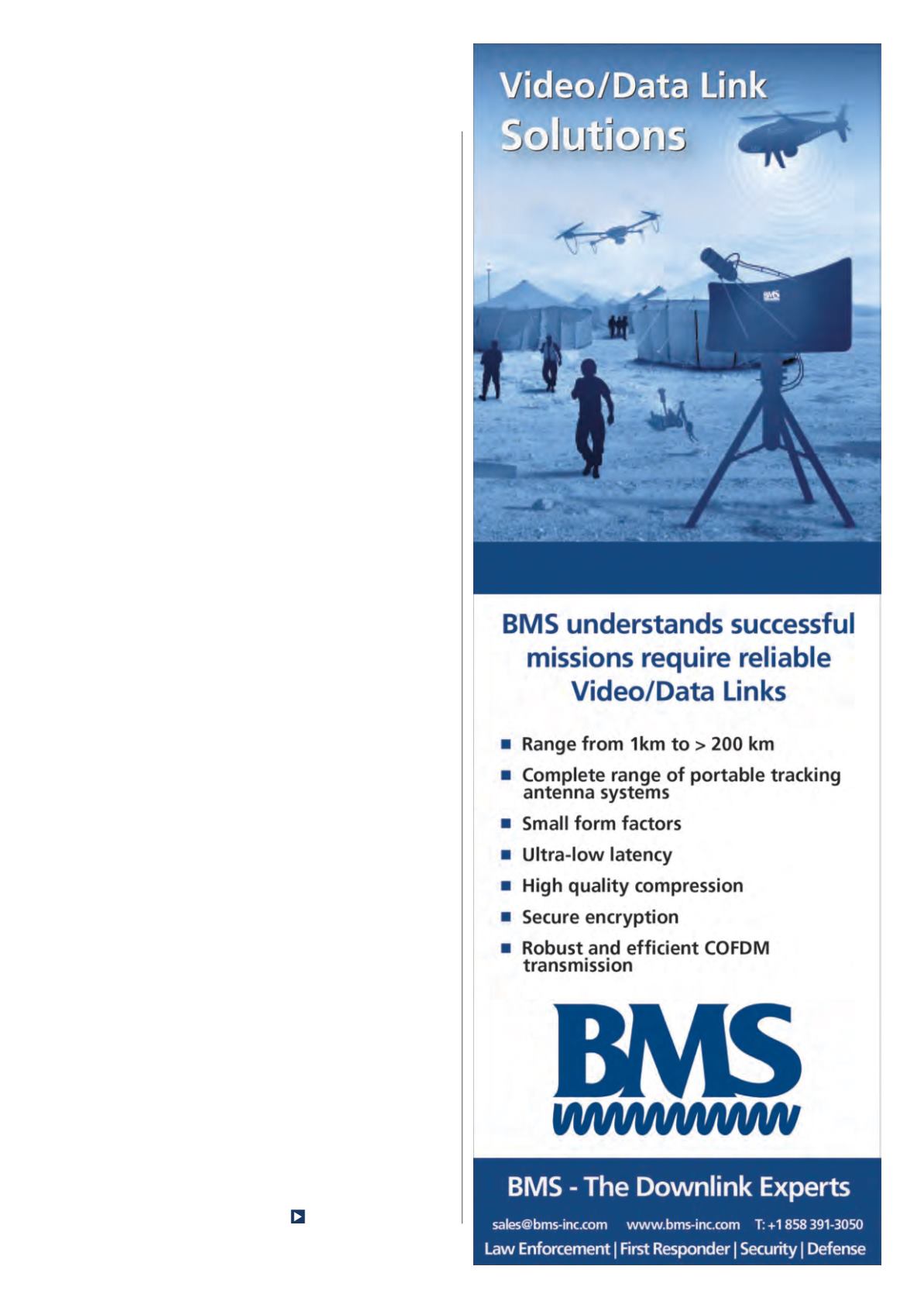
anti-vibration mounting system with no
hard connection between the engine
and the mount (which is hard-mounted
to the bulkhead with screws), a new
exhaust system and other changes. The
2.0 litre composite fuel tank is built into
the airframe and is connected to the
carburettor by a short tube.
With the three-blade fixed-pitch
propeller attached, the power plant has
generated around 4 kg of static thrust
in tests. Running on the bench at the
planned cruise rpm of 5000, Alti has
achieved more than six hours’ endurance
with a fuel load of only 1.8 litres of
standard unleaded petrol.
For the moment, the engine does not
charge the batteries in flight as there is
no need, but the company is considering
this for future versions. It is in talks with
a local hydrogen fuel cell manufacturer
and may integrate a small fuel cell to
run the electrical system and charge the
batteries in flight to enable mid-mission
hovering and longer hovering endurance.
The batteries are the company’s own
brand of lithium-polymer units, and have
a capacity of 6000-8000 mAh from eight
cells connected in series. They power
custom-built U7 motors from T-Motor,
which are screwed down to a mounting
base in the carbon pods via anti-vibration
mounts. The motors drive carbon fibre
rotors from the same company, which is
currently testing 16 and 18 in versions.
Advanced electric motors
T-Motor’s latest U7 V2.0 motors are
available in 280, 420, 490 KV variants,
KV being shorthand for the relationship
between rpm and voltage. Low KV ratings
indicate high torque, and a 420 KV motor
will theoretically turn at 10,500 rpm with
no load; speeds naturally come down
with the aerodynamic loads generated
by the propeller. T-Motor recommends
420 and 490 KV motors with the above
propeller/rotor sizes.
The U7 V2.0 range is built in a 12N14P
configuration, indicating a 12-tooth
stator and 14 magnets. With a 6 mm
shaft diameter, the 420 KV U7 for