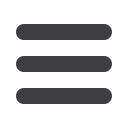
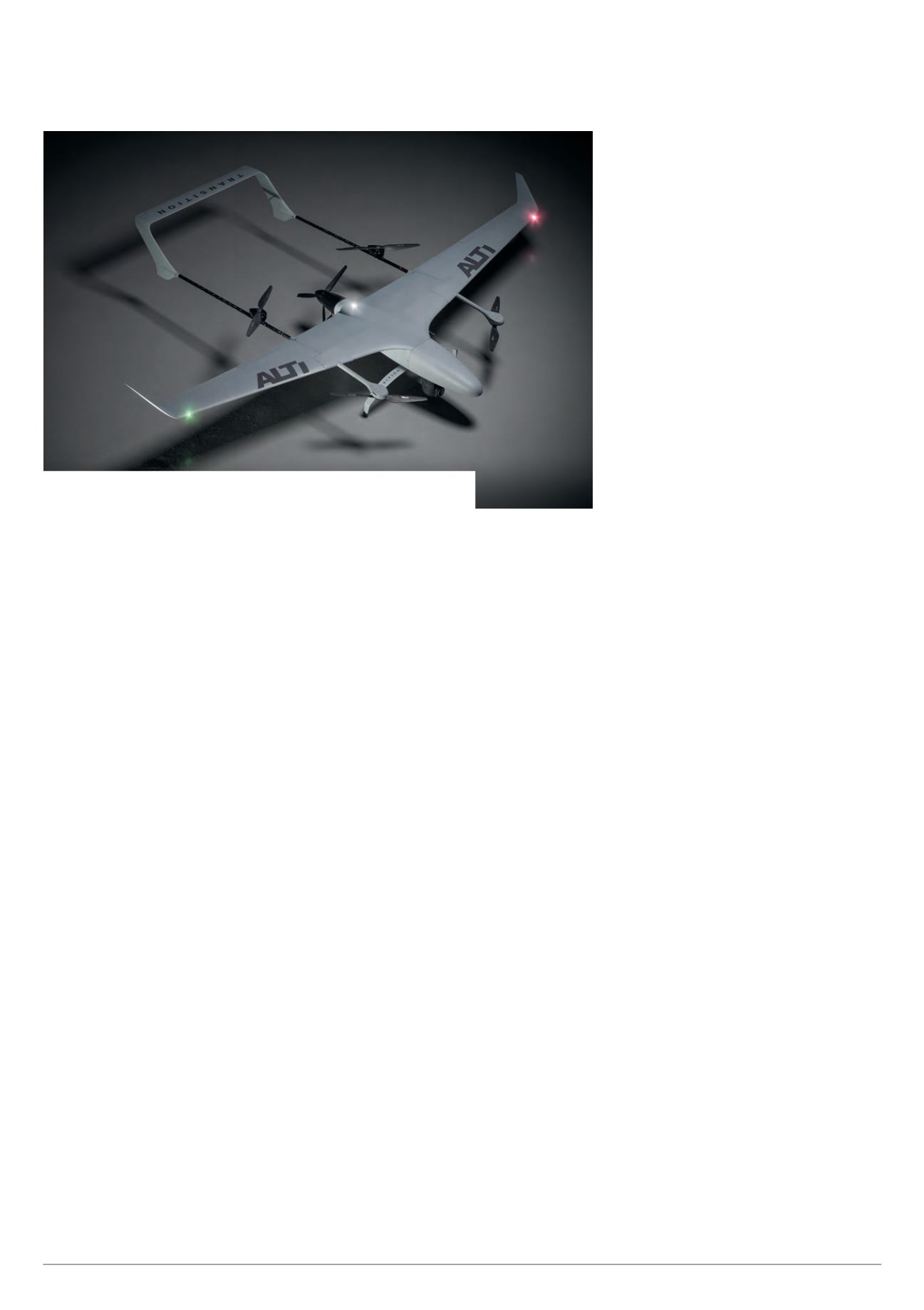
26
The ends of the carry-through spar
in the fuselage and wing root structure
mate with concentric stub spars bonded
into the outer wings, while carbon studs
locate the outer wing sections to prevent
them from rotating about the spar
ends. The pods containing the electric
motors are moulded into the optimum
aerodynamic shape, while the tail booms
are simple carbon fibre tubes made with
a 6k weave, which means there are 6000
filaments per tow or fibre bundle from
which the part is woven.
There are no mechanical hinges on
the airframe due to integrating Kevlar
hinges for all the control surfaces into
the primary skin laminates. The primary
benefit is toughness, as minor impacts –
or bird strikes, says de Villiers – no longer
threaten the loss of a control surface,
while localised punctures or other field
damage can be patched simply.
No metal is used in the structure, so
most fasteners tap into machined plastic
tapping plates bonded to the inside
of the structural skins, while the stub
spars in the wings have a metal thread
bonded in with epoxy resin to take the
wing-retaining aluminium finger nut. The
landing gear legs are also moulded in
carbon fibre and are shaped to produce
lift in forward flight.
Pre-preg laminates
To ensure a consistent ratio of epoxy
resin matrix to reinforcing fibre, Carbonix
uses a pre-impregnated (pre-preg)
laminating system, while curing at
high temperatures guarantees stability
in hot operating environments, and a
nano-toughened formulation improves
resilience in bonding areas.
De Villiers says Carbonix sources
its carbon fibre from several suppliers.
Specialised weaves come from SGL
group in Germany, which also supplies
Airbus and BMW, and from GMS in
Australia. Surfacing pre-pregs, meanwhile,
come from Lavender Composites, which
for example offers a variant of ACG’s
ZPREG range, as used by Ferrari.
To form deeply curved parts such as
fuselages, a plug or pattern is machined
from plastic or tooling board, then a Gurit
epoxy tooling system is used to make
the mould from the same material as the
final part to ensure consistent thermal
expansion of tool and part at high cure
temperatures.
For prototype tooling, the company
relaxes the tool specifications but adds
an epoxy gel coat to give a hard, non-
porous tool surface for production.
With flatter parts such as wings and
control surfaces, it mills the female mould
directly from aluminium or steel using
CNC machinery to provide an ideal hard
and durable tool surface. In some cases
matched moulds are used to give both
sides of a part a smooth finish.
Instead of using an autoclave, parts
are cured in vacuum bags in an oven,
because for thin parts excessive pressure
can degrade structural performance
by decreasing the moment of inertia of
lightweight skins.
Saito four-stroke single
The thrust motor is a single-cylinder
Saito FG21 spark ignition four-stroke
engine with over-square bore and stroke
dimensions of 32 x 26 mm for a capacity
of 20.52 cc. The piston has a single ring
for compression and oil control, and the
valves are operated by pushrods driven
by a cam geared to the crankshaft and
rockers with valve clearance adjusters.
The engine weighs about 620 g.
With an operating speed range of
1800-9500 rpm, it runs on 91 octane
unleaded petrol pre-mixed with high-
quality synthetic two-stroke oil at a ratio
of 20:1; Saito recommends Evolution
Oil’s EVOX1001Q. This mixture is fed to
the cylinder via a floatless carburettor
supplied by a negative-pressure
diaphragm pump.
Saito provides its own ignition system
consisting of the ignition box, earth, sensor
and spark plug wiring and a switched cord
for connection to the battery. The company
also provides its own
¼
-32 spark plug
designated SAIG20120.
The Alti Transition has a three-blade
propeller, and the FG21 is designed
to drive units of 15 in in diameter with
pitches between 7 and 9 in. (Pitch is a
measure of how far the propeller would
move forward in one revolution if it were
a screw in a solid material.)
Alti has made a number of
modifications to the FG21 to suit it to
its new home. The carburettor has
been moved inside the fuselage,
as has the ignition module, driving
changes to the way it connects to the
cylinder. There is also a new custom
June/July 2016 |
Unmanned Systems Technology
Dossier
|
Alti Transition
Transition’s electric lift motors also provide hover yaw control. In production
versions, the rears will be integrated into the centre body/wing root section