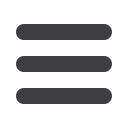
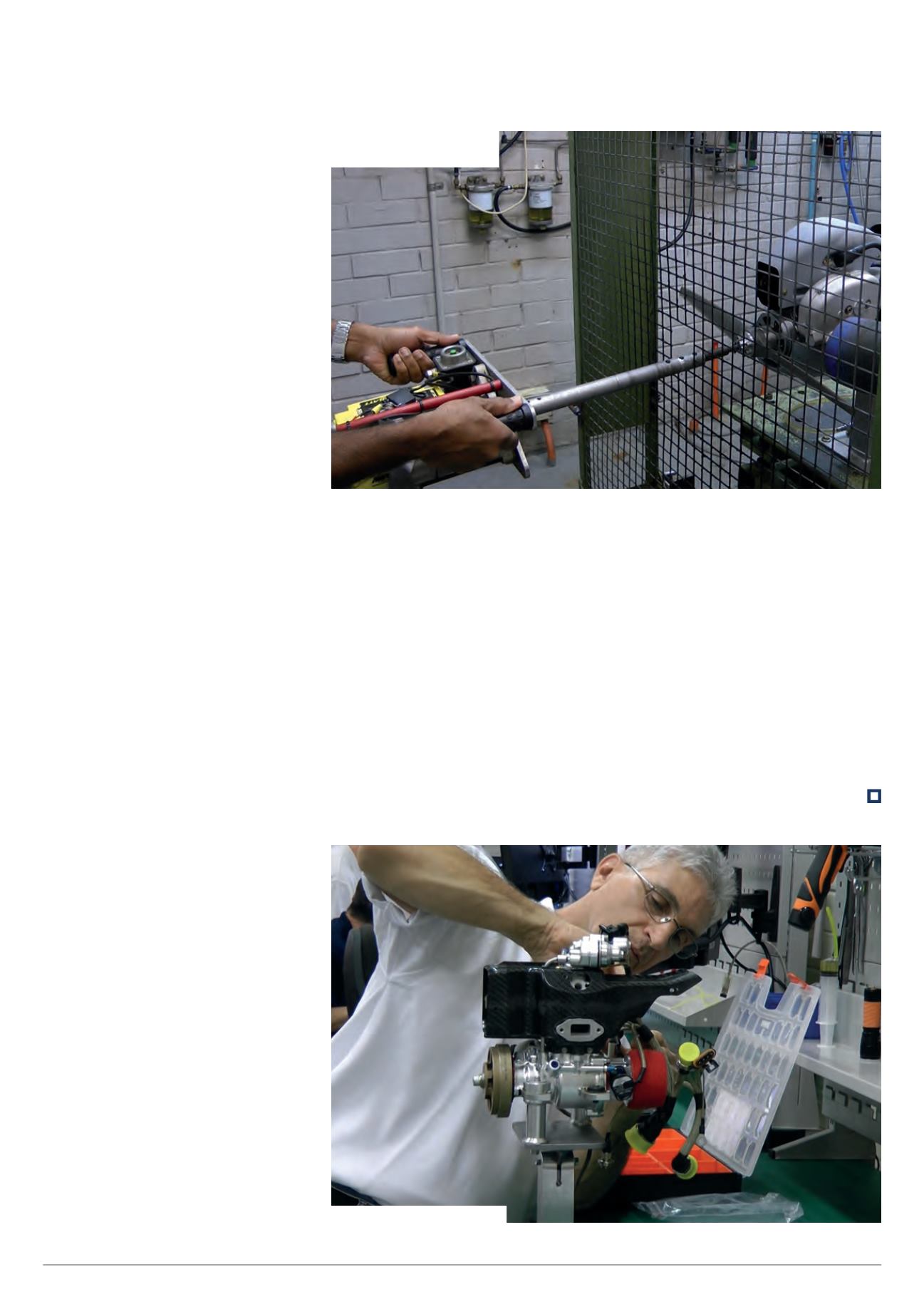
69
Insitu N20 UAV 50 cc two-stroke single
|
Dossier
the oil metering pump. It incorporates
logging of key engine parameters, and
all sensors have redundancy. The ECU
has what is described by Cathcart as
“advanced diagnostics”.
The ECU stores all engine data, while
selected information is transmitted to the
operator in real time. A diagnostic port
allows data to be downloaded directly
from the ECU when the craft is parked.
Data from all operations is logged,
with software run on the operator’s PC
automatically able to recalculate the life
of individual components in the light
of ongoing operation and providing
diagnostic information.
Thus can the operator carry out their
own checks and any required field
maintenance. The only routine between-
service replacement items are the
air filter and the spark plug, and both
are accessible by removing the cowl.
Extending the time between overhauls
was a key target, to minimise the need
for field maintenance.
“A lot of incidents are post-field
maintenance,” notes Beloy. “Through
robust design we have minimised the
in-field maintenance requirement – even
our muffler is maintenance-free.”
The N20 in operation
The N20 project began in mid-2012, and
Orbital’s UAV engine division – Orbital
UAVE – started design work in July 2013,
just after being awarded the contract.
At the start of the project Orbital used
rapid prototyping to create representative
engines to investigate aspects such
as bore and stroke possibilities; this
validated its simulation work.
The first proper prototype was
assembled in time for bench testing
at Insitu in June 2014. The engine was
certified as flightworthy in January 2015,
and was first flown in April 2015. The final
prototypes – production-representative
engines – were built at Orbital in
December 2015. By the end of 2015 the
development programme had used
dozens of engines, and there had been
over 7000 hours of test running.
Orbital had run numerous durability
tests, matching FAA requirements for
manned aircraft engines, and the N20
had come through with flying colours.
The aim is to be prepared to certify it
for aviation use should the FAA’s remit
be expanded to include engines for
unmanned aircraft, which is anticipated
in 2017. “This could be the first engine
certified for unmanned use,” says Beloy.
“Already we have achieved our
durability target – now we will see how
far we can go,” he adds. “In the past we
have seen detonation in a conventional
spark ignited jet fuelled two-stroke but
not in this engine, even when we have
pushed to try to induce it.”
The N20 runs from 3000 to 6500 rpm
and is rated at 2.4 kW at 6500 rpm take-
off power. It cruises in the 3500-6500
rpm range and can operate from -30 C
to +49 C and at altitudes up to 20,000 ft.
Thanks to its innovative design around
Orbital’s unique FlexDI technology, it
promises to set a new benchmark for
engines of its type.
Unmanned Systems Technology
| June/July 2016
An external starter is used to
fire up an N20 on a test rig
Assembly of an N20 at Orbital