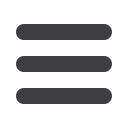
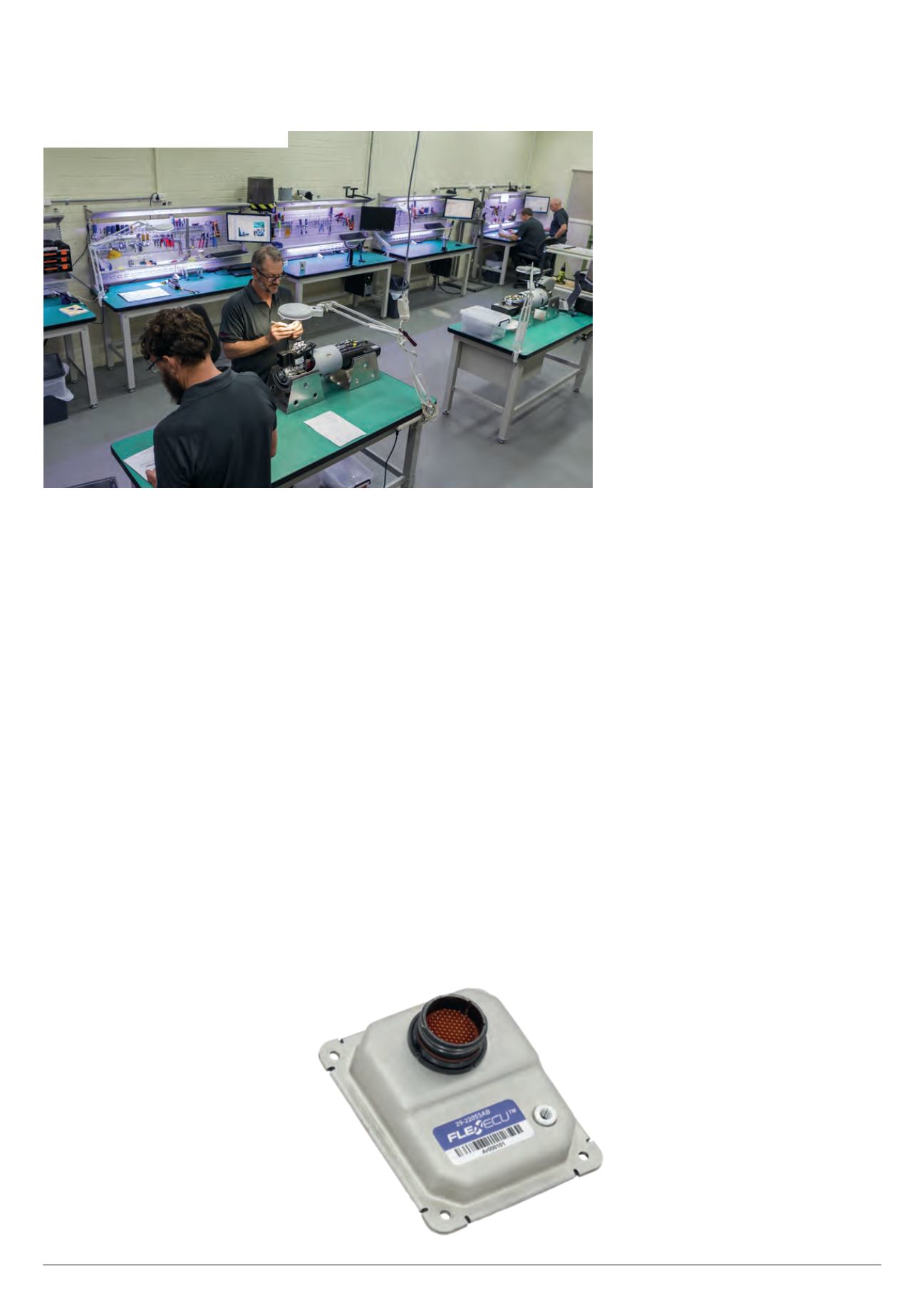
68
undisclosed. Also undisclosed are the
surface treatments applied to the piston
skirt, crown and ring groove.
All Cathcart will say is that “the piston
design minimises thermal expansion,
and the cylinder design [with integral
head] ensures that the bore stays closer
to round when hot. That means we can
run a tight clearance between the skirt
and cylinder, maximising heat transfer,
resulting in a cooler-running piston and
enhancing durability.”
The single ring is chrome-plated steel
with a symmetrical barrel profile. Its other
design features are undisclosed. Cathcart
does report though that the manufacture
of the ring, the piston and the cylinder
are such that ring end-gap adjustment is
not required during assembly.
Lubrication, cooling
and exhaust
Engine lubrication is total loss, with an
electric oil metering pump controlled
by the ECU such that its supply varies
in accordance with the requirements of
speed and load. The supply line from
an external oil tank housing the pump
serves various galleries in the crankcase,
with Cathcart unwilling to disclose the
oiling arrangement in detail.
“There is no spray jet involved, but the
key is in where the galleries release the
oil as the crankcase pressure pulses
above and below atmospheric,” he says.
“All the lubricant ends up as an oil mist
within the crankcase and, having made
its way to the combustion chamber, is
either burned or simply expelled as part
of the scavenging process.”
In the interest of noise attenuation the
muffler is of a ‘multi-pass’ type, which
means that the exhaust gas has a much
longer exit path than appears to be the
case when viewing the engine. Cathcart
explains that it consists of inner and outer
shells forming acoustic chambers and is
“without any service items inside – there
are no absorption items to get blocked”.
The clever compact muffler bolts directly
to the barrel, with no other support, hence
no danger of thermal expansion causing
cracking. “This approach is simple and
robust,” Cathcart observes.
All cooling is obtained from air flowing
over the engine. In a pusher configuration
the cooling duct intake faces the
oncoming airflow with its exit just ahead
of the propeller. That means the propeller
pulls air through the duct, ensuring a
supply even when the craft is stationary
before take-off with the engine running.
The duct directs air over the combined
head and barrel, and its effective size
is not adjusted in flight, when it benefits
from the ram-air effect of the craft’s
forward motion; there is an additional
ram-air cooling flow to the power supply
unit. The charge air filter does not have a
forced supply, it breathes from ambient
air within the engine compartment.
Electronics
The generator creates a three-phase
alternating current that is rectified to dc
by the power supply unit (PSU), which
provides a 14 V output to the engine bus
and a 28 V output to the bus serving
the rest of the craft. Those outputs are
separately controlled by the engine’s
management system, while the PSU has
the ability to operate on two-phase input
should one of the generator’s phases fail.
There is no battery in the engine’s
power supply system; the PSU takes
power from the generator as required.
The mechanical load thus imposed
on the engine is proportional to the
electrical load, where torque is inversely
proportional to engine speed. The
generator is sized for the maximum
requirement of the entire craft.
The ECU reacts to the instantaneous
demand for current from the PSU and
adjusts engine power accordingly, via the
fuelling or the throttle position. Unlike the
throttle, the FlexDI fuelling provides scope
for an instantaneous reaction to any
change in loading from the generator.
Developed specifically for UAV
applications, the Orbital ECU operates
the coil(s), the two injector solenoids,
the throttle servo, the fuel pump and
June/July 2016 |
Unmanned Systems Technology
N20 engine assembly at Orbital in Australia
The compact Orbital FlexDI engine control unit