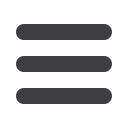
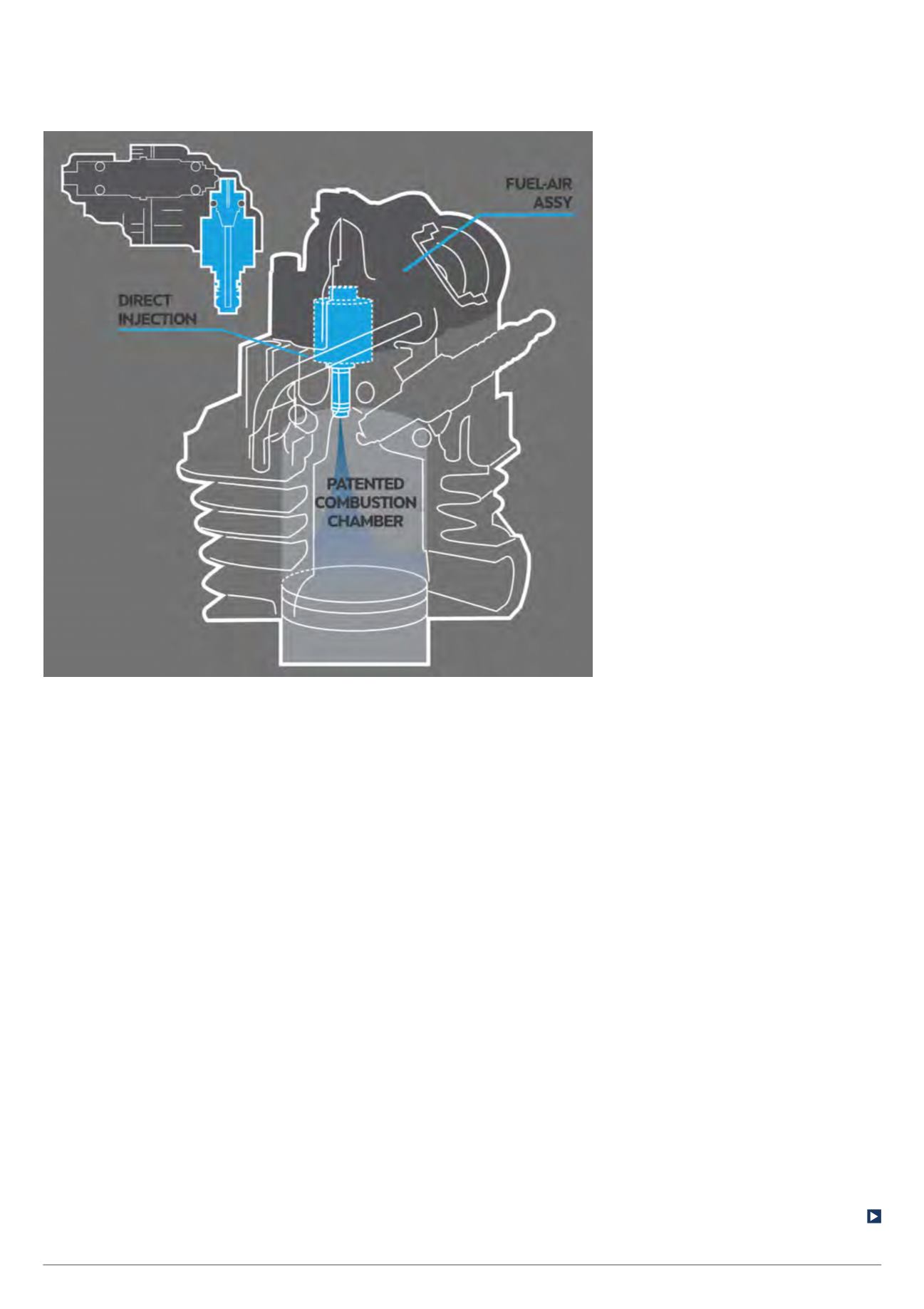
60
Dossier
|
Insitu N20 UAV 50 cc two-stroke single
existing engine used in the ScanEagle,
Insitu wanted a larger displacement for
greater take-off power, and for the same
cruise power level to lower the engine’s
operating speed. That in theory would
enhance reliability and fuel efficiency,
and reduce vibration and (propeller and
engine) noise levels. Running slower also
allows use of a larger diameter propeller,
which is more efficient as well as quieter.
Consequently the move was made
from a 28 cc to a 50 cc displacement.
Beloy says, “The weight penalty
associated with that increase is marginal
considering the improved specific fuel
consumption provided by Orbital’s direct
injection system. Moreover, the larger
displacement of the N20 can provide
additional climb power for heavier
payloads, for more extreme applications
as well as significantly more electrical
power for more demanding payloads.”
FlexDI
Orbital calls its unique compressed-air
assisted DI, which is used in conjunction
with its own spark ignition and engine
management systems, FlexDI. The
engine management system embraces
its own ECU, sensors and attendant
actuators. It has had a number of
different applications, starting with a two-
stroke Mercury marine engine in 1996
and including high-volume applications
such as two-stroke scooters made by
Aprilia and Piaggio. Its reliability and
effectiveness are thus well proven.
There have been two- and four-stroke
applications of FlexDI. Orbital’s chief
technology officer Geoff Cathcart admits
that over the years the advantage of
FlexDI has proved greater in two-stroke
than in four-stroke applications. Typically,
he says, a two-stroke switching from port
injection can obtain a 50% reduction in
fuel consumption and a 90% reduction
in emissions.
He explains that in the case of a
port injected two-stroke, a significant
proportion of the fuel-oil mixture in the
incoming charge is lost from the cylinder
through the exhaust port during the
scavenging process. Using FlexDI instead
there is no fuel in the charge during the
scavenging phase, and excess air can
be used to help extract spent gas.
The basic approach to injection is that
of stratified charge combustion, with the
incoming fuel being spray-guided. The
ingress of fuel is assisted by a dedicated
compressed air supply running through
the delivery nozzle. The pressure of the
compressed air transports the fuel into
the combustion chamber, in the process
creating very small droplets.
Cathcart says, “Think of an aerosol
spraying a very well atomised mist.
The air accelerates as it expands,
and that acceleration shears the fuel
droplets, creating a very finely atomised
mist. Compared with the 120 microns
representative of port injection, our
average fuel droplet size is 8 microns,
which is the industry benchmark.”
Cathcart notes that in the case of
conventional high-pressure direct
injection, the fuel is broken up by fine
holes in the delivery nozzle, which
doesn’t inherently create as good
atomisation as FlexDI.
“Rather than having an inward-opening
nozzle with many small holes, our
outward-opening pintle acts like a poppet
valve, forming an annulus through which
the fuel is sheared by the action of the
compressed air. Our fine atomisation
results in better vaporisation through
increased surface area of the fuel,” he
says.
“Heavy fuel is less volatile than
gasoline, so is much harder to spark-
ignite. Given our droplet size, spark rather
than compression ignition works fine.
Owing to the atomisation we obtain, and
the fact that we keep the fuel off the cold
bore wall, heavy fuel can be spark ignited
down to -30 C in 5 s or less without
the need for a glow plug or similar. Our
stratified combustion provides a wide
June/July 2016 |
Unmanned Systems Technology
Schematic of Orbital’s FlexDI compressed-
air assisted direct injection