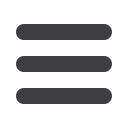
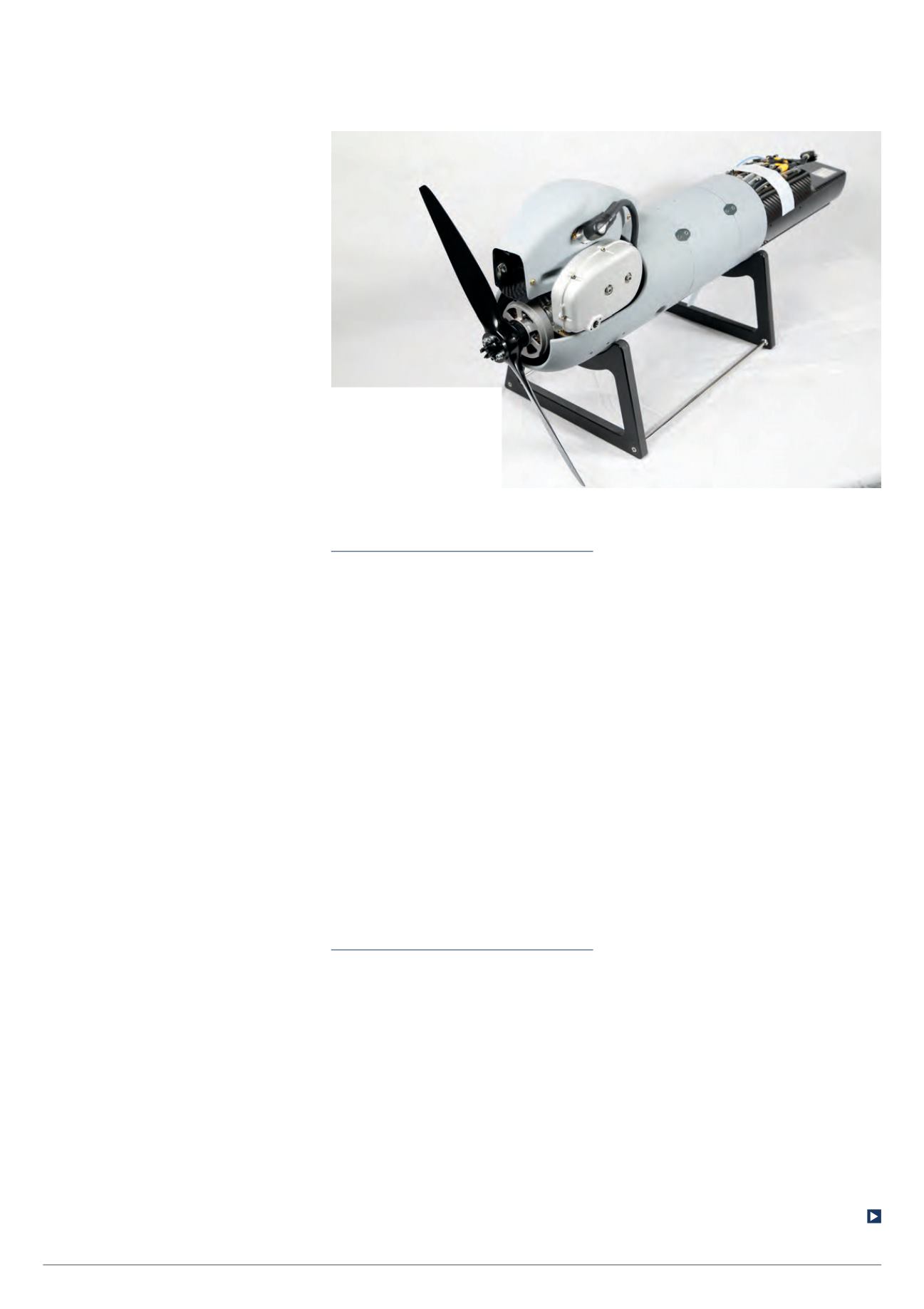
59
were already a leader in reliability
through development of the existing
engine, but we wanted to push the bar
with the N20. The goal is zero engine
failures, especially as any failure can
cause the loss of an expensive payload.
“We have more than 20 years of
learning from the development and
operation of our existing engines. The
N20 is a combination of our experience
and that of Orbital.”
Overseen by Insitu, Orbital drew the
N20 from the aforementioned clean sheet
of paper. Since Insitu funded the project
it owns the IP, aside from the proprietary
incorporated Orbital DI technology.
The 50 cc N20 produces 2.4 kW. It
runs on Jet fuel (A, A1, JP5 and JP8)
while an N21 version runs on certain
types of gasoline or Avgas, although the
only difference between the two is in the
engine calibration firmware. The engine
is air-cooled, has an upright cylinder and
is used as a pusher in the ScanEagle (in
other words, the propeller is at the rear).
The engine core has been designed
to be adaptable to a variety of airframes,
of which the ScanEagle is the first. The
engine core is augmented by a fuel
supply system, an oil supply system,
a muffler, a generator, a propeller
and an engine management system.
Orbital supplies the fuel pump, the
fuel injector and the ECU while Insitu
has collaborated with a propeller
manufacturer to develop an application-
specific item.
“The N20 has already met all its targets
in respect of power, fuel consumption
and reliability,” Beloy reported as
this article was being written, and
preparations were in hand for the first
production examples to begin operation.
Engine design
considerations
We asked Beloy, given the clean-sheet
approach, why not opt for a change
of engine type, perhaps to something
more radical?
“Reliability is the chief requirement,”
he explains. “There was the temptation
to use something different but it was
considered more important to use well-
proven technology.” Supercharging and
turbo-supercharging were ruled out on
grounds of cost and reliability, as well
as added weight, size and complexity.
“We make sufficient power without the
additional complexity,” he says.
A compression ignition engine would
require a higher compression ratio,
and with that a stronger, heavier engine
architecture, and it would create more
vibration, hence the preference for
continuing with spark ignition. “However,
it must in all circumstances be possible
to ignite jet fuel in a controlled manner,
and Orbital’s technology does this,”
Beloy emphasises.
Spark ignition of jet fuel normally implies
running hot, which in turn causes the
build-up of deposits in the combustion
chamber. That not only reduces the time
between overhauls but also brings a
danger of pre-ignition. Orbital’s technology
makes the engine run cooler, overcoming
this drawback. It also helps meet the key
challenge of the vast range of operational
conditions to which the ScanEagle is
subject, from the cold of the Arctic to the
heat of the desert.
The ScanEagle has always been
powered by an air-cooled two-stroke single.
It was originally powered by a modified
model aircraft engine, although that 28 cc
unit has been much modified over time.
Insitu wanted to stay with an air-cooled two-
stroke in consideration of power density.
Minimising weight was a key target,
hence the continuing use of just one
cylinder. Compared with a twin, a single is
lighter and more fuel-efficient. It also implies
a craft with less aerodynamic drag and
helps make the engine more affordable.
However, compared with the
Insitu N20 UAV 50 cc two-stroke single
|
Dossier
Unmanned Systems Technology
| June/July 2016
We wanted to
push the bar
with the N20.
The goal is zero
engine failures,
especially as any
failure can cause
the loss of a
costly payload
The powertrain package
for Insitu’s ScanEagle UAV
incorporates the N20 into a
module that can be removed
from the craft without
disconnecting any fluid lines