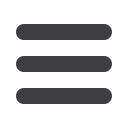
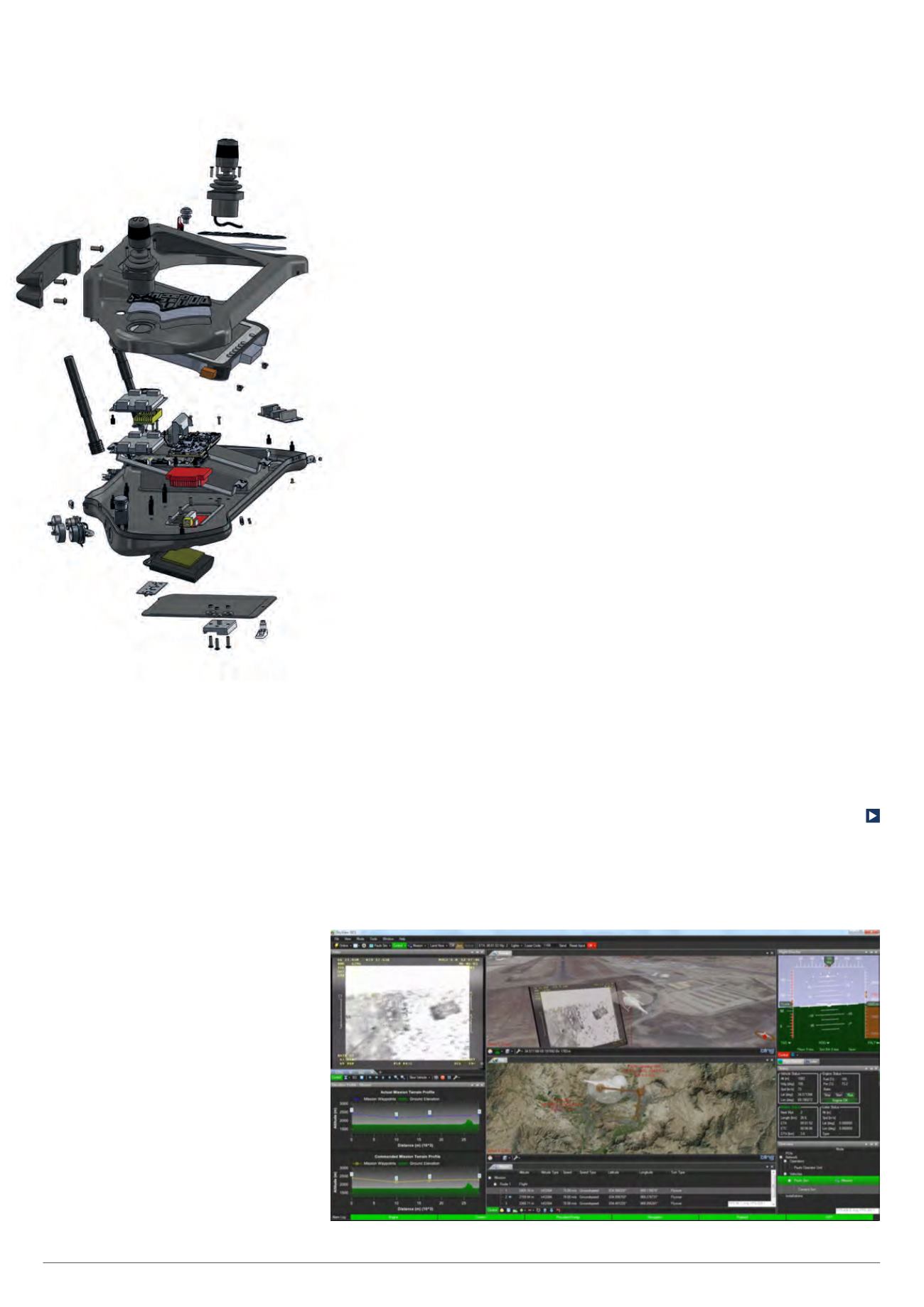
34
Focus
|
Ground control systems
the craft, while the second screen can
display the data from the payload, usually
still and video imagery. Unlike a small
UAV mission though, these GCSs need
to be set up quickly, and the operators
sit at them for many hours, so a larger
screen size has to be supported.
The requirement for these screens
is not necessarily high resolution but
high brightness, especially if operating
outdoors, so the two screens need a
brightness of 1500 nits (the common
measure of brightness equivalent to
1 candela/m
2
) compared with a
consumer monitor at 500 nits. There is
another issue in that the monitors have
to be able to operate down to -20 C, and
most commercial screens cannot do this.
The single-screen version implements
a ‘picture-in-picture’ to combine the
two. It is seen as more portable, being
battery powered, while the dual and
triple screens are used for system
development or missions of more than
an hour, so have a more static control
centre often powered by a generator.
Many GCS designs for smaller
unmanned systems are based around
a commercial ruggedised laptop
running the Windows operating system,
with custom power subsystems and
interface cards. This provides the latest
microprocessor technology such as the
Intel Core i5 processors in a casing that
is dust-, water- and vibration-proof to the
IP65 standard, and drop-proof from a
height of up to 180 cm.
The systems are designed to operate
in temperatures ranging from -20 C
to +60 C so that they can be used
anywhere from the desert to the poles,
but this requires the use of components
such as high-temperature electrolytic
capacitors on the motherboard that are
not necessarily used on commercial
boards. This though allows the fully
ruggedised models to comply with the
MIL-STD 810G military standard for
reliability.
Using a commercial PC platform allows
the GCS provider to easily upgrade the
performance of the system and simplifies
the addition of peripheral boards. These
can all be added via the USB ports
and controlled with existing C libraries,
making the software development
simpler than with a fully custom design.
With 2.4 GHz processors, the platform’s
response time of 30 ms is sufficient to
provide the control to the unmanned
craft, as this is largely about setting
waypoints for the navigation system
and autopilot on the craft. This comes
from using a mature operating system
such as Windows 7 and the software
development skills to ensure that
unnecessary operations do not interfere
with the critical control paths, and is
one reason for the transition to the latest
operating system, Windows 10, being
slower than on the desktop PC.
Power
Keeping the GCS powered depends
on the way the system is configured.
For long missions, operators and data
analysts are seated at the terminal and
use power from a generator; with shorter
missions, with a man-portable GCS,
multiple standard battery packs are
used. These are connected to a ‘hot-
swappable’ interface board that allows
one battery to be removed and replaced
with a fresh one without interrupting the
operation of the mission.
Two battery packs can provide six to
seven hours of power, enough for most
flights. However, operations in remote
areas may not be within range of a
cellular network, so the ground station
may store the data locally for analysis
later. The GCS in this scenario will
struggle to link back to the cloud, so
additional wireless connectivity such as
a satellite link may be needed, and
June/July 2016 |
Unmanned Systems Technology
The assembly of a single
screen GCS (Courtesy
of Flying Production)
Using split-screen display software allows
a single-screen GCS to display data from a
range of sources (Courtesy of UAS Europe)