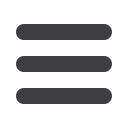
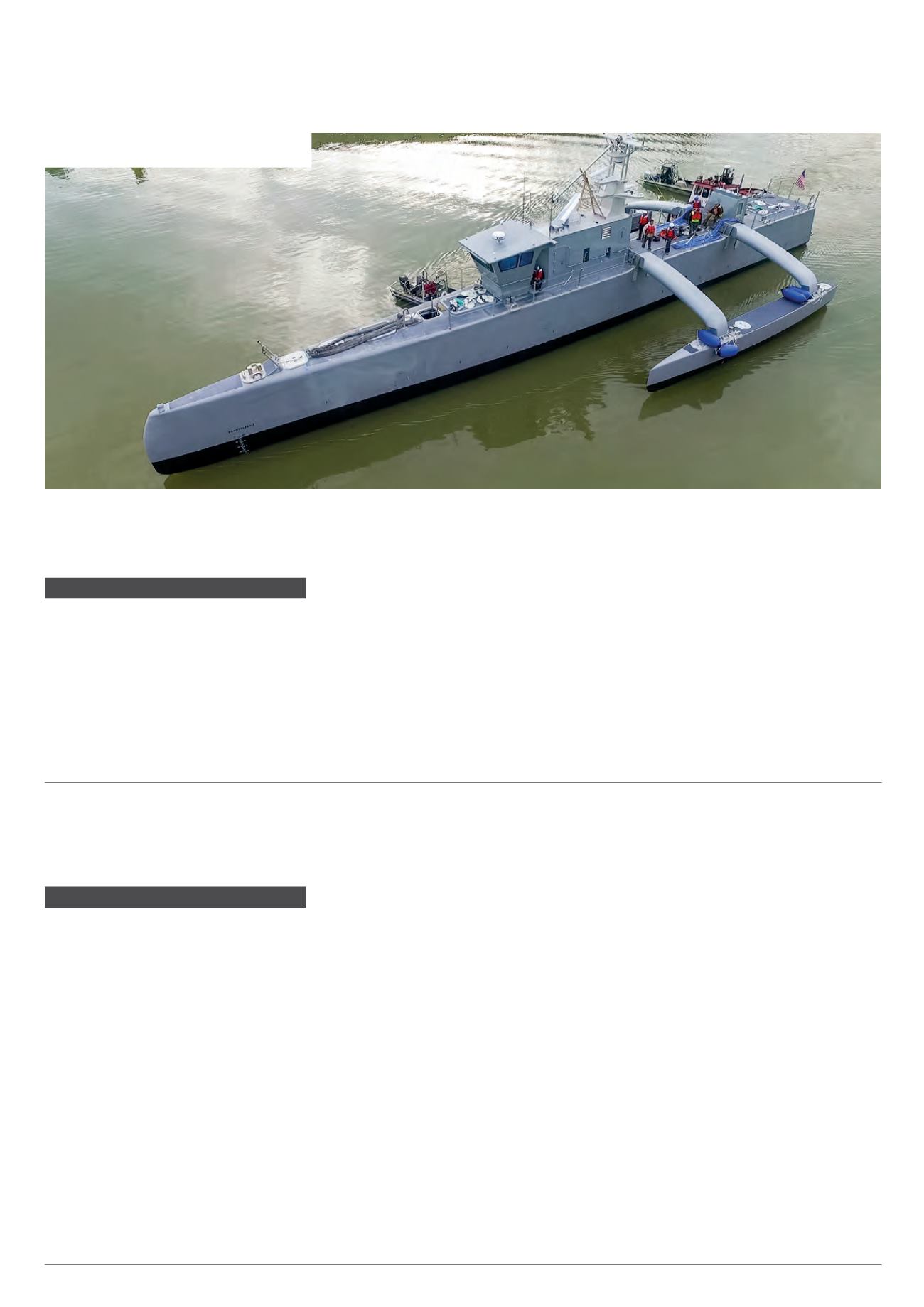
10
Platform one
June/July 2016 |
Unmanned Systems Technology
The world’s largest autonomous system
has started two years of trials. Called
Sea Hunter, it is a 40 m ship for tracking
diesel submarines (writes Nick Flaherty).
The sensor and autonomous control
systems were developed by engineering
firm Leidos under contract from US
research agency DARPA, and the vessel
was commissioned for use in April. It
will now undergo two years of testing at
San Diego, California, using a removable
operator control station and a person on
board for safety and reliability testing, but
it is intended for fully autonomous use.
The vessel is designed to stay at
sea for months at a time with up
to 40 tonnes of fuel. It can track a
submarine at speeds of up to 27 knots
in all weather conditions using a hull-
mounted modular sonar system from
Raytheon that is integrated with the
Leidos control system.
It costs around $20,000 a day to
operate, compared with $700,000 a day
for a destroyer, and each ship will cost
around $20m.
Defence
Sea Hunter is designed for submarine tracking
at up to 27 knots in all weather conditions
Sub tracker begins trials
The Southampton University Laser
Sintered Aircraft (SULSA) has been
tested by the Royal Navy in the Antarctic
to help with navigation (writes Rory
Jackson).
It marks the most rigorous trial yet
for the world’s first 3D-printed UAV
since it was unveiled in mid-2011. A
Mobius ActionCam in the nose of the
craft captured the surroundings of ice
patrol ship
HMS Protector
, from which
it was launched, with data recorded to
a microSD card. After completing its
mission, SULSA was retrieved from the
water and later re-launched.
“We intend to add video downlink
capability in the near future, and future
variants may incorporate more thorough
waterproofing and design changes to
enable recovery to a ship,” said Andrew
Lock, enterprise fellow at the university.
The 3 kg craft features elliptical wing
planforms and a geodetic airframe,
printed from Nylon 12 in just five parts
over 24 hours. Such a complex design
would have been expensive and time-
consuming without the combination
of CAD and selective laser sintering,
and the structure snap-fits together in
minutes, requiring no fasteners or tools,
even when attaching payloads.
This enabled operators to strip SULSA
down entirely and re-assemble it after
retrieval. “A bayonet fit, which allowed
quick access to the avionics, would have
been difficult to produce conventionally,”
Lock said, “and a hydrophobic coating
on the avionics meant most components
were re-usable.
“We also heated the pitot tube to cut
the risk of ice build-up by physically
connecting it to the ESC [electronic
speed controller].”
The consistency of the printing process
also allowed previously unflown airframes
to be deployed without needing to trim
control surfaces or adjust autopilot gains.
Navy tests 3D-printed UAV
Assisted navigation