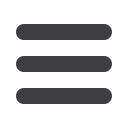
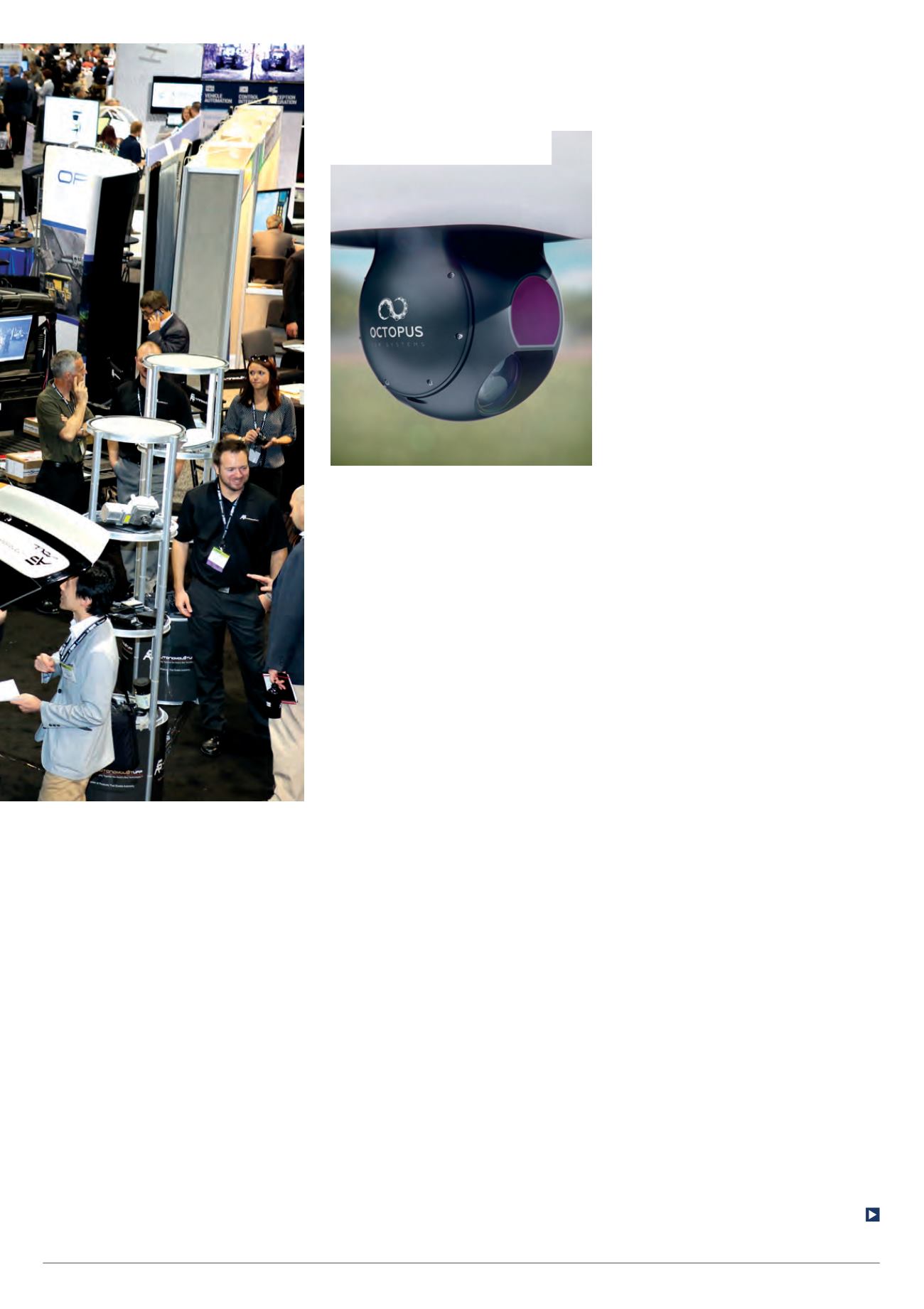
43
control stations developed for its UAVs.
While UAV Factory will concentrate on
developing craft such as the Penguin
UAV profiled in our first issue, this
new Octopus division is expanding its
offerings with a tracking antenna and a
gimbal launched at the show.
The new gimbal is known as the
Epsilon 140, in reference to its 140 mm
diameter, and contains stabilised day and
night cameras. Ozolins noted that the
package includes what he describes as
advanced image stabilisation and a very
powerful video processor.
He added that the Epsilon 140 is the
only micro-gimbal on the market which
has an onboard moving target indicator.
“When you have a wide field of view,
a person, for example, or a car or an
animal a couple of kilometres away
might account for only a couple of pixels.
But this software identifies any movement
between that object and the background,
highlights it for the operator, and having
‘seen’ it the operator can then zoom into
it to see if it is of interest.
Flyability announced the launch
of “the world’s first collision-tolerant
flying robot”, Elios (previously known
as Gimball) at the show to herald the
700 g, spherically caged quadcopter’s
transition to serial production by the
end of the year. This follows five years
of development through seven design
generations for Elios, whose diameter
of less than 400 mm enables it to fit
through manholes and access hatches
to inspect confined spaces in power
plants, pipe and cable tunnels, and
ships’ holds for example.
The Swiss company’s co-founder
Patrick Thévoz told us that the cage is
made from carbon fibre-reinforced plastic
rods joined into hexagonal modules
by 3D-printed reinforced plastic nodes.
(These nodes are the only remaining
3D-printed parts, as the company is
moving to faster techniques such as
injection moulding for mass production.)
The modules are held together by
ties so that damaged sections can be
replaced quickly in the field, while the
rods have a softer coating to protect from
impacts with sharp edges. The cage is
designed to absorb impacts with objects
at speeds up to the robot’s software-
limited maximum of 15 kph.
Inside the cage, the UAV is mounted
on a three-axis gimbal that mechanically
decouples it, allowing the cage to roll
over or around objects while the UAV
with its HD video and thermal cameras
remain stable, turn on the spot with the
robot and tilt independently to be aimed
at inspection targets.
The 2.4 GHz radio link works in a
licence-free band and uses multiple
antennae, COFDM and advanced signal
processing “to ensure that we will not
lose the signal as soon as we enter a
metallic environment or get out of the line
of sight”, Thévoz said.
Control software has to be adapted
to a robot that experiences very
strong disturbances to its attitude from
collisions. Also, the aerodynamics of a
robot compact enough to fit into such a
small sphere are complex because of
interactions between overlapping rotor
blades, their close coupling to the body
of the UAV, their high rotational speed
and thrust density, and the aerodynamic
effects of the cage.
A new development from
MicroPilot, Kyle Hayes reported, is a
tablet/smartphone version of its well-
established ground control software.
This, he said, is in response to customer
demand – using the software on a tablet
or even a phone rather than a PC gives
the operator more freedom to move
around while operating a craft.
This version, still in development at the
time of the show, is fully touchscreen, and
Hayes demonstrated how a waypoint can
be relocated using this approach.
The design is such that thumb control
is the primary tool, so that a tablet can at all
times be held firmly in both hands.
“You can control the flight, operate a
payload and so on using your thumbs,”
Hayes noted.
AUVSI’s Xponential
|
Show report
Unmanned Systems Technology
| June/July 2016
The Epsilon 140 from UAV Factory has
stabilised night and day cameras